NCBI Bookshelf. A service of the National Library of Medicine, National Institutes of Health.
National Research Council (US) Chemical Sciences Roundtable. The Role of the Chemical Sciences in Finding Alternatives to Critical Resources: A Workshop Summary. Washington (DC): National Academies Press (US); 2012.
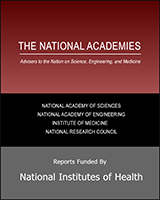
The Role of the Chemical Sciences in Finding Alternatives to Critical Resources: A Workshop Summary.
Show detailsA major use of critical materials is in catalysis, which is the subject of both this chapter and the next chapter. Catalysts can be used on a large scale, as is the case with many heterogeneous catalysts, or on a small scale, as is the case with most homogeneous catalysts. A critical element may not be the most costly component of a catalyst, but the availability of that element or sudden changes in cost can disrupt its use. For example, as described in this chapter, platinum-based catalysis and electrocatalysis hold particular promise in several energy technologies, but platinum falls into one of the highest levels of criticality, as described in the previous chapter. Major research efforts are therefore under way to reduce the use of platinum in catalytic processes and to develop replacements for platinum in various applications.
CRITICAL MATERIALS IN CATALYSIS
“Catalysis is a broad topic, one that covers many orders of magnitude, from the 5-million-pound-per-hour scale down to the gram scale,” explained James Stevens. However, catalysts can be divided into two main divisions, homogenous and heterogeneous catalysis, each with its own issues for critical materials.
In terms of volume, most catalysts are heterogeneous catalysts. Heterogeneous catalysts are easy to separate from product, and they work at very high temperatures, with alumina and silica catalysts capable of operating at temperatures of 1000°C. Heterogeneous catalysts are challenging to study and afford a poor degree of synthetic control. However, if heterogeneous catalysts could be rationally designed, they could offer tremendous advantages—for example, in emissions control applications.
Homogenous catalysts are more sophisticated chemically and can perform more useful chemical reactions. They are more selective and produce higher reaction rates than heterogeneous catalysts, and it is possible to design complex structures for specific tasks and use high-throughput, combinatorial methodologies to discover new homogenous catalysts and new reaction schemes that use new homogenous catalysts. However, homogenous catalysts are limited to use in lower-temperature chemical reactions.
Homogenous catalysts are by their nature used in very small amounts and produce many moles of product per mole of catalyst, with very high reaction rates. For example, a chiral ferrocynal iridium phosphine catalyst, used in the largest application of asymmetric synthesis to perform an enantioselective hydrogenation as part of an herbicide synthesis, produces over 2 million turnovers per catalyst molecule at a rate of 600,000 per hour (Blaser et al., 1999). Producing 10 million kilograms of product per year requires about 5 kilograms of iridium, assuming that no recycling occurs. This catalyst accounted for about 0.1 percent of U.S. imports of iridium in 2010.
Costs and the Supply Chain
While the 5 kilograms of iridium used per year in this catalyst would cost about $100,000, again assuming that no recycling occurred, that would account for less than 30 percent of the cost of the catalyst (Blaser, 2002). The most expensive components of this catalyst are the ligands surrounding the metal, which is often the case with homogenous catalysts. In addition, although the metal can usually be recycled, the ligands cannot. Other examples showing that ligand costs can dominate catalyst costs include a constrained-geometry titanium catalyst for ethylene co-polymerization; a zirconium catalyst for isotactic polypropylene synthesis (for which the metal accounts for about only 0.5 percent of the total catalyst cost); and a rhodium catalyst for enantioselective hydrogenation (for which the metal accounts for less than 15 percent of the total catalyst cost).
These catalysts are expensive to produce for several reasons. They are made in very small quantities, and small-scale production tends to be expensive. In addition, these catalysts often require multistep syntheses, which add cost.
Even though the metals in homogeneous catalysts are usually not the most expensive component, the cost of these metals can fluctuate wildly. Rhodium prices, for example, increased 20-fold during a four-and-a-half-year period starting in early 2004, jumping from $16,000 to $314,000 per kilogram. Prices then plummeted in a matter of months to under $50,000 per kilogram. Stevens explained that price increases are not necessarily a bad thing for a big chemical company. When prices increase, the metal the company has in storage also increases in value, producing a gain in working capital. When the price plummets, as it did with rhodium, the result is a loss in working capital. Some of these short-term fluctuations can coincide with the startup of a new large chemical process and the purchase of these metals to have in inventory.
The supply chain for these metals is global and involves several players. As an example of how the supply chain operates, Stevens used a hypothetical case in which Dow Chemical developed a new process that required 100 kilograms of platinum. The platinum-group-metal inventory and purchasing manager at Dow would contract with one of the many precious metal brokers to either purchase or rent the necessary platinum, depending on the prevailing market conditions or whether the company wanted to hedge the price of platinum. After acquiring the metal, the company would send it to a catalyst manufacturer who would prepare the catalyst according to Dow’s specifications. Once the catalyst was spent, or inactive, it would be sent to a refiner to recover the platinum. Often, the broker, catalyst manufacturer, and refiner are the same entity. For platinum-group metals, loss of metal is on the order of 1 to 2 percent. Small amounts of metal also can be recovered from the reaction vessels and pipes in the chemical plant once the plant is decommissioned.
Cost and Supply Constraints
Catalysts used in refineries, Stevens noted, have particular issues because of the enormous quantities of catalysts used, often on the scale of millions of kilograms. Fluid-cracking catalysts and isomerization catalysts, for example, require very large amounts of metal. Sometimes a process that looks promising becomes impractical because of the amount of metal it would require. In one instance, a superior iridium-based fluid-cracking process would have required more iridium than is available worldwide. These facts point to the enormous potential for catalysts that do not require platinum-group metals.
However, in trying to develop replacements, it is important to keep an eye on the real market drivers. As an example, Stevens cited the enormous effort that went into creating simple metallocene catalysts based on titanium and zirconium to produce isotactic polypropylene with a melting point of around 160°C. This effort took 15 years, cost $500 million, and was successful, but the catalysts are not used commercially, except for one catalyst used to make a very small amount of a specialty material.
One promising area is the development of hydrosilylation catalysts that do not require platinum-based metals. Hydrosilylation is the largest-cost application for homogeneous catalysis. Platinum-based hydrosilylation catalysts are used widely in pharmaceuticals manufacturing, while rhodium-and platinum-based catalysts are used to make siloxanes and silicone rubber. As a result of the catalytic process used to make cured silicones, for example, some 4 to 6 metric tons of platinum per year are “lost” with the product (Figure 3-1). At the current price of platinum, that amount represents $250 million to $377 million worth of metal, a cost industry swallows because of the catalyst’s superior properties.

FIGURE 3-1
Current hydrosilylation processes lose some 4 to 6 metric tons of platinum per year. SOURCE: T. Don Tilley, University of California, Berkeley (Stevens, 2011).
The development of lower-cost catalysts that meet critical performance characteristics could have significant economic benefits. However, the cost of the metal is not the only factor that must be considered. A catalyst that uses an inexpensive metal but expensive ligands could end up costing the same. Stevens elaborated to say that the current platinum-based catalyst is used because it has the desirable cure kinetics that enable the polymer to remain liquid for the time necessary to fill a mold. It also produces regioselectivity and chemo-selectivity, resulting in high-molecular-weight polymers, which is a critical parameter.
Potential approaches to meeting these requirements with a lower-cost catalyst include identifying new silane and olefin activation chemistries and new reaction mechanisms that do not require the two-electron redox processes catalyzed so effectively by platinum. The application of new high-throughput catalyst discovery methodologies holds promise for making such advances.
Another promising area is the development of new catalysts for acetic acid production, the second largest use of homogeneous catalysis. In the 1960s, BASF launched an acetic acid process that used a cobalt catalyst, but this was replaced in 1970 with Monsanto’s greatly improved rhodium-based catalyst. The new catalyst was more highly selective and required lower pressures, reducing overall costs per pound of acetic acid. Rhodium recovery was also very high.
This catalyst, however, was replaced in the 1990s by an iridium-based catalyst developed by BP. This catalyst, which could be used in the same plant as Monsanto’s rhodium-based catalyst, had higher selectivity still and afforded better water use, thereby lowering the capital costs associated with drying columns. The lower capital costs more than made up for the increased cost of the metal used. Iridium, unlike rhodium, is not at the moment considered a critical material because it is not used in significant quantities today. If demand for iridium increases significantly, it could be considered a critical element.
The latest version of this catalyst, introduced a decade ago by Celanese, uses rhodium again but offers better iodine and water management and allows for larger plant construction. This, in turn, lowered the cost per pound of the final product. Though rhodium is a critical material, the amount used by the chemical industry to manufacture acetic acid is relatively small.
Emissions Catalysts
Emissions catalysts, particularly for use in cleaning up diesel exhaust, are significant users of platinum-group metals. Diesel is growing as a percentage of vehicle production worldwide, largely because of the higher fuel efficiency of diesel engines. However, diesel exhaust also has significant emissions problems. Removing NOx from diesel exhaust requires a reduction catalyst and is difficult using existing catalyst technology, whereas removal of carbon monoxide and unburned hydrocarbons requires an oxidation catalyst (Figure 3-2). Particulates must also be removed from diesel exhaust, and filters contain metal catalysts.

FIGURE 3-2
Removing pollutants from diesel emissions requires several catalysts and filters. SCR: selective catalyst reduction; LNT: lean NOx trap. SOURCE: Stevens (2011).
Today, emissions catalysts account for 81 percent of U.S. platinum-group metal imports. Emissions catalysts also use significant quantities of cerium, which acts as an oxygen buffer in NOx reduction. Looking ahead, new filter structures will require new catalysts, and there are opportunities to develop catalysts that do not use platinum-group metals. Nickel-based catalysts may prove useful, as may copper-based catalysts now that concern over the potential to produce dioxins as a byproduct has been alleviated.
Hydroformylation and Enantioselective Catalysis
The biggest application of homogeneous catalysis, in terms of the amount of product made, is in hydroformylation. The first catalysts were rolled out in the 1940s and used cobalt, a first-row transition element. Cobalt catalysis suffered from the need for high pressures and temperatures, poor conversion and low selectivity, and costly catalyst recovery (Figure 3-3). Poor selectivity was the real problem because it is expensive to separate chemicals, in terms of both energy and capital costs. The major application of this technology was to make linear molecules, either n-butanol or derivatives such as 2-ethylhexanol, and copper-based catalysts resulting in normal-to-iso ratios of 3 to 4.

FIGURE 3-3
Cobalt catalysts produced undesirable amounts of iso-butanol compared to n-butanol. SOURCE: Stevens (2011).
In the 1970s, Union Carbide commercialized a rhodium-based hydroformylation catalyst. While more expensive, this catalyst operated at much lower pressures and temperatures and generated product with a normal-to-iso ratio of 10, reducing capital costs substantially. Union Carbide introduced a more expensive rhodium-based catalyst in 1995 that required still lower temperatures and pressures and generated product with a normal-to-iso ratio of 30. This catalyst is more expensive because it uses phosphite ligands rather than low-cost phosphine. Today, 95 percent of the 7 million metric tons per annum production of 2-ethylhexanol and butanols is achieved using rhodium-catalyzed hydroformylation.
“The challenge in all of these systems,” Stevens explained, “is to control the regioselectivity, chemoselectivity, and enantioselectivity, where enantioselectivity refers to making the branched molecule, which has a chiral center, versus the normal molecule, which does not.”
Today, there is a big push to develop catalysts that make more of the branched, chiral products than the normal products (Figure 3-4). Research has shown that the electronic environment surrounding the rhodium metal controls whether the product is the branched or linear isomer.

FIGURE 3-4
Hydroformylation can produce linear or branched isomers depending on the ligands surrounding the rhodium catalytic center. SOURCE: Stevens (2011).
Branched aldehydes are incredibly versatile chemical intermediates that can be used to produce a wide variety of compounds, but the key is controlling regio selectivity and enantioselectivity. Today, researchers at Dow and Union Carbide have developed a number of ligands that achieve these requirements, though the application of high-throughput methods could improve catalysts further. These catalysts use rhodium or cobalt, but again, it is the ligands that ultimately determine the selectivity that the catalysts display.
By developing a better understanding of the mechanisms by which the catalysts work, researchers have been able to rationally design ligands to improve catalyst performance. As an example, Stevens discussed how Dow chemists took ligands developed by DuPont and created a new set of ligands that improved catalyst performance. The initial ligand, called DuPhos, showed good enantioselectivity in asymmetric hydroformylation, but the catalysts had poor activity. Dow chemists asked if the activity could be improved by increasing the electron-withdrawing substituents on the ligand, and the answer was yes. The resulting diazophospholane ligands not only improve catalyst activity but also provide the opportunity to fine-tune reactivity because their basic chemical skeleton can be readily modified. They are also easy to synthesize in what is essentially a two-step process that combines an aldehyde, benzoic acid, and hydrazine to make large libraries of molecules.
Today, with the large number of hydroformylation ligands available, it is possible to generate very high branched-to-linear ratios and very high enantioselectivities with high turnover rates and under mild conditions. There is still room, however, to improve the chemoselectivity and functional group tolerance. “The key is to find out the critical performance characteristics needed for commercial viability,” said Stevens.
Finally, Stevens noted that there is real need for high-performance catalysts that can provide enantioselectivity around a carbonyl bond. Catalysts now available achieve turnover numbers on the order of 10 to 1,000 s−1 and function at very low rates.
ALTERNATIVE MATERIALS TO REPLACE PLATINUM IN CATALYTIC AND ELECTROCATALYTIC APPLICATIONS
In the quest for secure sources of energy, the conversion of renewable resources into liquid fuels—biomass into diesel and gasoline, for example, and water into hydrogen—is among the most active areas of research. Platinum-based catalysis and electrocatalysis hold particular promise in producing renewable, domestic sources of transportation fuels and other basic chemicals, but platinum is a strategic, imported metal. In the case of electrocatalysis, said Jingguang Chen, efforts are ongoing to reduce the amount of platinum needed by a factor of 10 to produce hydrogen via the electrolysis of water. For the catalytic conversion of biomass into liquid oxygenates, research is focusing on completely replacing platinum with tungsten in the necessary catalysts.
As has already been highlighted, platinum-group metals are used widely in the chemical and refining industries. In the area of clean energy technologies, platinum is the most promising catalyst for low-temperature fuel cells, electrolyzers, and photoelectrochemical cells, which use sunlight to power electrolysis. These clean-energy catalysts, however, require larger platinum nanoparticles than are needed in traditional heterogeneous catalysts, which would boost platinum use dramatically. Indeed, recent studies, said Chen, suggest that there is not enough platinum in the world to use such catalysts on the scale envisioned to power industrial processes.
The major challenge in replacing platinum with an early transition metal is that the electronic properties are different. Many research teams are attempting to use carbon to modify the electronic properties of tungsten and other metals that, like platinum, are in the 5d group of metals. In particular, metal carbides have many properties desired for industrial heterogeneous catalysts. They have high hardness and wear resistance, are stable at high temperatures, and are excellent electrical conductors. Using theory and model systems, researchers have developed design principles that have enabled them to create new metal carbide catalysts that have platinum-like activity and stability.
Efforts to reduce, rather than eliminate, platinum use are focusing on creating thin-layer or monolayer supported catalysts. This approach takes advantage of the fact that platinum catalysis occurs only on the very top layer of a platinum particle (Figure 3-5).

FIGURE 3-5
Thin-film and monolayer catalysts can greatly reduce the amount of platinum needed for catalysis. ML: mono-layer SOURCE: Esposito and Chen (2011).
Hydrogen Production from Water Electrolysis
One rationale for developing efficient methods of generating hydrogen via water electrolysis is that hydrogen could then be used to store intermittent solar or wind energy. Electrons would be harvested during production and used to electrolyze water, producing hydrogen that would be stored and converted back into electricity using a fuel cell at night or when winds are calm. The major obstacle to this scenario is that large-scale commercialization is impossible because of the demand for and cost of the platinum catalysts now used in electrolysis and fuel cells.
There are two ways to use sunlight to power electrolysis. The indirect method is to use photovoltaic panels to convert sunlight into electricity that then is used to electrolyze water. The direct method is to use a catalyst that generates electrons directly from sunlight and uses those electrons to produce hydrogen and oxygen from water. Both processes require platinum in the cathode.
As part of a concerted effort to develop a monolayer platinum cathode for electrolysis, Chen and his collaborators asked the following questions:
- What is the descriptor responsible for making platinum the optimal catalyst for the hydrogen evolution reaction?
- Does monolayer platinum on a tungsten carbide particle meet such a descriptor for high activity in the hydrogen evolution reaction?
- Is monolayer platinum on a tungsten carbide particle stable under the relatively harsh conditions of the hydrogen evolution reaction?
The key feature of the descriptor comes from research on the binding energy of hydrogen to various metals. These experiments show that the hydrogen binding energy with platinum is −0.46 electron volts (eV). Quantum calculations are used to predict which carbides and monolayer systems would produce a hydrogen binding energy similar to that seen with platinum. Tungsten carbide alone has a predicted hydrogen binding energy of −0.99 eV, but when combined with a monolayer of platinum, the predicted hydrogen binding energy drops to −0.43 eV.
Chen and his collaborators confirmed these predictions experimentally. Tungsten carbide alone, which costs four orders of magnitude less than platinum, is inactive electro-chemically. However, electrocatalytic activity increased as the density of platinum on a tungsten carbide electrode increased. When the platinum density reached one monolayer, electrocatalytic production of hydrogen was virtually identical to that seen with pure platinum.
Chen noted that platinum binds very tightly and stably to tungsten carbide. Furthermore, extended electrolysis tests showed that monolayer platinum on tungsten carbide structures was stable. Hydrogen production remained constant, and physical characterization using scanning electron microscopy and x-ray photoelectron spectroscopy confirmed that the platinum monolayer was stable on tungsten carbide under the harsh electrolysis conditions. In fact, said Chen, the platinum monolayer on tungsten carbide material is more stable than the commercial catalyst used today.
Thin films such as these are useful for experimentation and model calculations, but platinum monolayers on supporting particles would perform better in commercial applications. Chen’s group is using atomic layer deposition to form platinum monolayers on tungsten carbide particles and to create a commercially viable material after 10 deposition cycles. Electrolysis measurements show that the platinum-on-tungsten carbide particles produced after 10 atomic-layer deposition cycles are just as active as commercial platinum catalyst. However, elemental analysis reveals that these particles contain 10-fold less platinum than the commercial catalyst.
This is not the end of the story. The same binding energy model suggests, as Chen said, that “instead of just using tungsten carbides as a base material, we can actually think about other carbides, such as molybdenum carbides. We can even think about using palladium on metal carbides.” He also noted that this approach can be used to design platinum on metal carbide catalysts for other electrochemical devices, including their use as the anode material in direct alcohol fuel cells or the cathode material for oxygen reduction reactions.
Platinum-Free Catalysts for Biomass Conversion
In addition to his work on electrocatalysis, Chen and his collaborators have been developing platinum-free catalysts for converting biomass into oxygenated chemicals. These studies use quantum calculations and model systems to rationally design potential catalysts. Such studies enabled his group to develop a nickel-on-tungsten carbide catalyst that performs better and is more stable than a nickel-on-platinum catalyst for converting glycoaldehyde into hydrogen and carbon monoxide, which then can be combined using standard chemistry to produce a wide range of chemicals.
Though these examples show that it is possible to reduce or even eliminate platinum in industrially important catalysts, several challenges remain for these efforts to have a major impact. One is to increase the surface area of the platinum on metal carbide materials. Currently, high temperatures are needed to make stable metal carbides, but the resulting materials have low surface areas.
A related challenge is to develop new synthetic methods that create metal carbide with high surface areas, which would result in catalysts with much higher activity. Similarly, there is a need for better methods of depositing monolayers of platinum on metal hydrides while inhibiting carbon deposition on the particles, which reduces catalytic activity. A challenge in the electrocatalysis area is to develop platinum-sparing metal carbide materials that have long-term stability over a range of pH values.
DISCUSSION
In response to a question about whether there might be a balance between complete coverage of a metal carbide particle with platinum and somewhere between 25 and 75 percent coverage in terms of cost and stability, Chen said further tests may demonstrate that reduced coverage may be possible to achieve the same results. He explained that his group does not have the facilities to perform hundreds of hours of stability tests to determine the optimal coverage, and he hopes that a commercial vendor will be interested in conducting such tests. Chen also noted that recovering the platinum from these metal carbide materials appears to be easy.
Ernest Chamot, of Chamot Labs, asked if biomimetic approaches might be better than the rational design approach for creating new catalysts for biomass conversion. Chen replied that a biomimetic approach would likely work well for homogeneous catalysis. Such an approach would center on developing better ligands. For heterogeneous catalysts, however, a biomimetic approach is not likely to be successful.
Levi Thompson, Richard Balzhiser Professor of Chemical Engineering at the University of Michigan, and, with Thiel and Eggert, the third member of the workshop organizing committee, noted that his group has observed that the underlying metal carbide can actually dissolve under some conditions. He wondered if the highly oxygenated conditions in a biomass reactor would be conducive for dissolution of the underlying carbide, and he asked if Chen had observed that in his experiments. Chen replied that there is some tungsten dissolution, but only a small amount. The trick to suppressing dissolution, he explained, is to use very high pressures to compensate for oxidation.
In response to a question about the efficiency of biomass-to-chemical processes, Stevens noted that photosynthesis is actually very inefficient, using less than 1 percent of the incident energy. Even with sugar cane in the tropics, which is one of the best plants in terms of turning sunlight into useable materials, efficiency is less than 1 percent. As a result, making 700 million pounds a year of ethylene requires 450 square miles of sugar cane. “The net primary productivity of any plant-based photosynthetic process is a real limitation when you talk about the scale that’s required to make chemicals on a big scale.”
Stevens also was asked what advice he would give a 22-year-old thinking about picking a research advisor, and he replied that industry is currently having trouble finding chemical engineers with the skills industry needs. He also thought that because the efficiency of photovoltaics is so much greater than the biomass conversion processes, photovoltaics would be the more promising field. Finally, over the next few decades basic research will remain essential for energy issues in areas such as the manipulation of matter on a small scale.
- Critical Materials in Catalysis - The Role of the Chemical Sciences in Finding A...Critical Materials in Catalysis - The Role of the Chemical Sciences in Finding Alternatives to Critical Resources
Your browsing activity is empty.
Activity recording is turned off.
See more...