NCBI Bookshelf. A service of the National Library of Medicine, National Institutes of Health.
Cieszynski A, Jung C, Schendel T, et al. Do-It-Yourself Products Fact Sheet: Default parameters for estimating consumer exposure – Updated version 2022 [Internet]. Bilthoven (NL): National Institute for Public Health and the Environment; 2022.
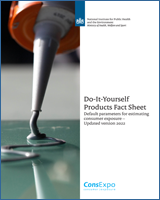
Do-It-Yourself Products Fact Sheet: Default parameters for estimating consumer exposure – Updated version 2022 [Internet].
Show detailsThe use of do-it-yourself products may result in either dermal, inhalation-related, oral, eye exposure or in a combination of these exposure routes. Users may be exposed during mixing and loading, during the application of DIY products as well as post-application. Most DIY products are ready to use, but some of them require mixing and loading prior to use. During the mixing and loading process, additional exposure may occur. The DIY products described in mixing and loading are glues (two-component glues, tile glue, wallpaper glue), fillers, two-component coatings, rust and paint removers and plasters made from powders.
In this Fact Sheet, the generic scenarios describe the use of the product, exposure conditions, as well as appropriate ConsExpo models to calculate expected exposure during the various stages of product use or the aftermath of the product use itself (e.g., clean-up phase). The various stages of product use that are considered generic for DIY products are:
- Mixing and loading (see subsection 4.1)
- -
powders
- -
liquids
- -
two-component products
- Application (see subsection 4.2)
- -
spray application
- -
adhesives
- Post-application
- -
clean-up phase (see subsection 4.3)
The current chapter only addresses generic default scenarios and their parameters, such as the mixing and loading of powder materials that are applicable to several products within this Fact Sheet. Chapters 6 to 12 provide the default scenarios, models, and parameter values (including those set in this chapter) to estimate the exposure in relevant exposure routes for the product categories mentioned in Table 3. Local eye exposure is not covered in this Fact Sheet because there is no model available in ConsExpo Web to derive this value.
Secondary exposure of bystanders may arise during and after DIY tasks have been conducted. Inhalation exposure may occur if another person is in the same room while the task is conducted. Dermal exposure can arise if a person tries to assist the user (pushing together freshly glued parts or cleaning up residues, e.g., wallpaper soaked with remover) or accidentally touches a treated surface or glued area after the task is completed. Nevertheless, in the following considerations regarding the default scenarios for different DIY products, the exposure of the user who carried out all contributing activities/tasks covers the secondary exposure during and after the DIY task, as well as the activities of any other person who takes over part of the tasks.
It is expected that the inhalation exposure of the user, who tends to be closest to the emission source, is higher than that of a bystander.
Therefore, once the inhalation exposure for the user is assessed, it can be assumed that the bystander’s exposure is covered by this value. Please note that inhalation exposure to volatile substances (e.g., solvents) may occur over a long period of time (days to months) after the application of the product. In some cases, this may lead to chronic effects. This potentially long period of time after use exposure is not in the scope of the default scenarios described in this Fact Sheet. If necessary, it has to be assessed separately, using individually adjusted assumptions and default values.
Similar considerations apply to the dermal exposure of bystanders/assistants. The main user himself will be much more dermally exposed than a person who occasionally helps out during the task. Furthermore, DIY products are designed to harden very quickly in order to, for example, make it possible to use a treated surface or a restored object again as soon as possible. Therefore, accidentally touching DIY products following completion of the task will result in low dermal exposure, compared to the exposure levels during use.
4.1. Mixing and loading DIY products
As mentioned above, several DIY products require pre-treatment handling before they can be used. The additional operations may lead to additional exposure from the product besides application. In this Fact Sheet, three mixing and loading processes are described. The first mixing and loading process describes the mixing of two components where inhalation can occur due to evaporation and dermal exposure due to spills or direct contact (e.g., adhesive putty) with the product (see subsection 4.1.1). Similar considerations are made below regarding the second mixing and loading process, covering the mixing of two liquids (see subsection 4.1.2). The dilution of powders in water is the third mixing and loading process. Dust particles from the powder may enter the breathing zone and hence lead to inhalation exposure (see subsection 4.1.3).
4.1.1. Generic exposure scenario for mixing and loading: two-component products
The mixing of two components to prepare an adhesive agent or filler may lead to inhalation and dermal exposure. The mixed components vary from (low viscosity) liquids to solids, but the mixing and loading process is regarded as similar. The two components are put together in a shallow mixing cup or a bucket (e.g., two-component parquet glue) according to the ratio provided by the manufacturer. Usually two-component products consist of a basis, the resin, and a drying siccative, which are then mixed with a spatula, with another kind of tool or by hand (adhesive putty) until a homogeneous mass is obtained. When mixed, the two components react chemically, and hardening can occur.
Inhalation
Inhalation exposure can take place if volatile compounds evaporate during the mixing process. The inhalation – exposure to vapour – evaporation – release area mode: constant model may apply here, where release from a constant area is considered. This model is selected as the default to describe the inhalation exposure from mixing and loading two-component DIY products.
Room volume and ventilation rate
Since the release of volatile substances from the mixing and loading activity occurs in the personal breathing zone, only this small area is relevant to inhalation. ‘Room volume’ is therefore interpreted here as personal breathing zone: a small area of 1 m3 around the user, relevant to the inhalation exposure for the short use duration in which the mixing takes place. A Q-factor of 1 is assigned because this is an assumption based solely on expert judgement.
A ventilation rate of 0.6 h-1 (te Biesebeek et al., 2014) for an unspecified room is used. This value reflects the default value for air exchange between the room and the outside environment, while the air exchange between the personal breathing zone and the rest of the room is not accounted for, mainly because of the briefness of the mixing effort. A Q-factor of 1 is assigned.
Mass transfer coefficient (MTC)
A generic default value for the mass transfer coefficient of 10 m/h is proposed. This generic default is usable for a situation where specific properties of the substance, the product and the indoor environment are not considered. The Q-factor is set to 2, because of the generic and conservative character of the calculation from which the default is derived.
For further explanations regarding the derivation of the default, please check the overarching issues document provided by RIVM (RIVM, 2018).
Release area
Evaporation of volatile substances is expected from the surface of the mixture in the used mixing vessel.
According to the total product amount that has to be mixed, the vessel may differ. For smaller tasks (total mixed product amount < 5 kg) a bucket with a 12-l capacity seems sufficient. Commonly used buckets in this dimension provide a constant release surface area of 800 cm2 (diameter = 32 cm), which is supported by information acquired in a short screening of the available products on the German market (see Table 121). For larger tasks (total mixed product amount > 5 kg) the vessel should provide enough capacity for 20 l product, which results in a release surface area of 1100 cm2 (diameter = 37.5 cm) (see Annex II A.5). Both release area values will be set as the defaults in the mixing and loading processes with the related dimension of product amount. Because mixing buckets with these specifications are commonly offered by most DIY retailers, the Q-factor for the default is set to 2.
Molecular weight matrix
The products available on the DIY market are mainly mixtures containing several constituents with different physicochemical properties. Because the evaporation process is not only determined by the substance of interest but by all compounds, the molecular weight matrix parameter is necessary. It is used to correct the evaporation rate since it describes the average molecular weight of the rest of the total product (product minus substance of interest). When the product only consists of substance, with a purity of 100%, this value can be left blank. However, in most cases the exact composition of a product is not exactly known. For this issue, a conservative default value of 3000 g/mol will be set, which is adapted from the Paint Fact Sheet where this value is used for solvent-rich paint. In this case, the main solvent is also the substance of interest, and its vapour pressure is not excessively influenced by other compounds in the paint because their concentration is expected to be rather low, or their molecular weight is very high. Further explanations regarding the molecular weight matrix are available in subsection 2.1.3 of the Paint Products Fact Sheet (Bremmer & van Engelen, 2007) and in the ConsExpo Web Manual (Delmaar & Schuur, 2016).
Dermal
Dermal exposure occurs when the two components are mixed together with some kind of tool. It is assumed that the surface area of two fingertips (small tasks; small mixing vessel, e.g., a cup) or of five fingers (larger tasks; bigger mixing vessels, e.g., a bucket) will be exposed from holding the tool or splattering. The dermal – direct product contact – instant application model is used to calculate the dermal exposure.
Exposed area
The fingertip is defined here as the top phalanx of one finger. According to the General Fact Sheet, the surface area of one hand (both sides) is 450 cm2 (te Biesebeek et al., 2014). Half this area is assumed to belong to the fingers, which equals 225 cm2. Consequently, the surface area of one finger is 45 cm2 divided into 3 phalanges (15 cm2 per phalanx). Therefore, the area of two fingertips, or rather top phalanges, is set at 30 cm2 (default). Some products have to be mixed in much larger quantities (> 1 kg). In those cases, the dermal contact area is much larger, and it is assumed that the surface area of all 5 fingers will be exposed (=225 cm2, see above) (te Biesebeek et al., 2014). An exception here is the mixing and loading of adhesive putty where extensive dermal exposure occurs while using just a small product amount (see subsection 6.5.2).
4.1.2. Generic exposure scenario for mixing and loading: liquid-liquid
Liquids are mixed in a suitable vessel. In most cases, this will be a bowl or a bucket, depending on the amount that needs to be mixed. The components will be poured into the mixing vessel either directly from the bottle or via an interposed measuring cup. It is expected that the physical efforts to homogenise two liquids are rather small. However, inhalation exposure may arise because of volatiles evaporating from the surface of the bottle opening/measuring cup and from the surface of the mixing vessel while the product is being homogenised. Moreover, the user can be dermally exposed during pouring and mechanical mixing through spills and spatters.
Inhalation
To calculate the inhalation exposure during mixing and loading within ConsExpo Web, the inhalation – exposure to vapour – evaporation – release area mode: constant model is used.
Room volume and ventilation rate
The defaults for the room volume and the ventilation rate are set according to the considerations made in subsection 4.1.1. The room volume is set to 1 mm3 (personal breathing zone), and the ventilation rate is 0.6 h-1. The latter value reflects the default value for air exchange between the room and the outside environment, while the air exchange between the personal breathing zone and the rest of the room is not accounted for.
Release area
Evaporation of volatile substances is expected from the open bottle and the surface of the mixture in the vessel. The surface of any measuring cup is neglected at this point because the substance will not remain in the cup for long. Therefore, this potential exposure source will be covered by taking into account the evaporation from the bottle opening, too.
It is assumed that the product is contained in a one-litre bottle that has a circular opening of 5 cm diameter and a surface area of 20 cm2.
According to the total product amount that has to be mixed, the vessel used may differ. For smaller tasks (total mixed product amount < 5 kg) a bucket with a 12 l capacity seems sufficient. Commonly used buckets in this dimension provide a constant release surface area of 800 cm2 (diameter = 32 cm) which is supported by information acquired in a short internet and on site (2 DIY markets) screening of the available products on the German market conducted by the authors of this report. For larger tasks (total mixed product amount > 5 kg), the vessel should provide enough capacity for 20 l product which results in a release surface area of 1100 cm2 (diameter = 37.5 cm) (see Annex II A.5). As the opening of the bottle (20 cm2) has to be considered too, the default release area for mixing and loading liquids amounts to 820 cm2 for smaller tasks and to 1120 cm2 for larger tasks. Because mixing buckets with these specifications are commonly offered by most DIY retailers, the Q-factor for these defaults is set to 2.
Dermal
To estimate the dermal exposure within ConsExpo Web, the dermal – direct product contact – instant application model is used for both direct pouring and loading with measuring cups.
Exposed area
It is assumed that direct pouring of liquids leads to dermal exposure on the side of the hand directing the bottle to the bowl or bucket. The default for the exposed area is set to be equal to one side of the hand, 225 cm2, which is in accordance with the General Fact Sheet (te Biesebeek et al., 2014). Since the assumption that one side of the hand is exposed is based solely on expert judgement (although the default for hand surface area is derived from a data-rich source), the Q-factor is set to 1.
Product amount – dermal
The Biocides Human Health Exposure Methodology Document (ECHA, 2015a) human dermal exposure to biocides during the process of dispersing a concentrate from a container and diluting it with water in a vessel. The 75th percentile for dermal exposure during this mixing and loading event is 0.01 ml, irrespective of the amount poured (ECHA, 2015a). Assuming a liquid density of 1 g/cm3, the default for the product amount landing on the skin during direct pouring is set to 0.01 g. Because of the availability of quantitative but specific (non-generic) and limited data (i.e., 4 measurements), the Q-factor is set to 2.
4.1.3. Generic exposure scenario for mixing and loading: powder liquid
During the mixing and loading process, powders may disperse into the air and can subsequently be inhaled or deposited on the skin. In the DIY sector, powder products are primarily meant to be mixed with water prior to usage, frequently in large quantities.
Inhalation
In the general mixing and loading scenario of a powder product, the powder is poured either directly from the package or with the help of a measuring cup into a mixing bucket. In the following considerations, no distinction is made between the two variations of pouring because they are not expected to result in exposure differences.
This Fact Sheet follows a different approach from the 2007 version (ter Burg, 2007) to describe the inhalation exposure while mixing and loading powders. The ConsExpo inhalation – exposure to spray – instantaneous release model (Delmaar & Schuur, 2016) is now recommended to estimate the exposure caused by inhalation of product particles. The physicochemical properties of solid aerosols emitted by sprays have much in common with the ones from powders, e.g., the very low volatility and their similar particle shapes. Although a powder is obviously not a spray, the instantaneous release of the spray model is thus best suited to approximate the exposure during the loading of powder. The release is expected to be very short-lived and therefore, the instantaneous release is preferred over the spray model. Default values are provided for the following model parameters for simulation of the generic scenario of exposure to powders (Meesters et al., 2018).
Frequency
In some cases, the amount of powder and water that needs to be mixed is too much to handle in one mixing effort. It is expected that the common DIY user will not have the equipment (automatic mixing device, sufficiently big mixing vessel) nor the physical properties (strength, endurance) in order to mix powder amounts that exceed 5 kg. Furthermore, it might become problematic to mix higher amounts because it is possible that the mixture will harden before it can be completely used.
Therefore, if the amount of 5 kg powder is exceeded, it is assumed that more than one mixing effort has to be conducted. The frequency of the mixing and loading scenario will then be set to be equal to the mixing repetitions that are required. If, for example, 30 kg powder have to be mixed with 7.5 l water, the frequency would be 6 times per event (event = use of tile glue, for instance).
Exposure duration
Specific data regarding the duration of mixing and loading filler products was recently gathered in a feasibility study. In total, there were 83 data points with a minimum of 0.5 minutes and a maximum of 20 minutes. The 75th percentile equals 3 minutes (Schneider et al., 2018). As there is no further data available for other DIY products, this value will be used as a default for the exposure duration taking into account the assumption that the mixing person is exposed during the whole mixing and loading process. The Q-factor is set to 2 because the parameter is based on only one source.
Released mass
Little information is available about the fraction of powder that is released to indoor air during mixing and loading powder products. Information on dust formation of washing powder is provided in the Cleaning Products Fact Sheet (Meesters et al., 2018; van de Plassche et al., 1999). The original experiments and home observation studies were performed by Hendricks (1970). The author found “that there is on average 0.27 µg detergent dust exposure per cup of product used”. Here, the detergent dust exposure refers to the amount of laundry detergent inhaled while “pouring the product from the carton into a measuring aid and then to the washing machine” (Burg et al., 1977; Hendricks, 1970; van de Plassche et al., 1999). It is possible to recalculate the supposed released mass in the experiments of Hendricks (1970) based on the laboratory conditions described (sampling time of 2 minutes, distance to dust source within personal breathing zone, inhalation rate of 16.3 l/min), by assuming that Cons Expo’s inhalation – exposure to spray – instantaneous release model (Delmaar & Schuur, 2016) is suitable for such a calculation and that the duration of the experiments is too short for the ventilation rate to be effective. The supposed released amount per cup (8.3 µg) is calculated as follows:
8.3 µg released mass per 200 g powder used will be used as the default value. The following assumptions are made in the calculation of the released mass: an instant release model is suitable for the calculation above, ventilation and gravitational settling of the dust is negligible for the exposure time considered and the short distance of the analytical device to the loaded powder directly leads to a release into the personal breathing zone of 1 m3. Because of these limitations, the Q-factor for this default is set to 1.
Room volume and ventilation rate
Room volume is interpreted here as the personal breathing zone, a small area of 1 mm3 around the user. Only this small area is relevant for the inhalation exposure during the brief time period that mixing and loading takes. The Q-factor is considered to be 1, because the interpretation of the personal breathing zone is based on expert judgement.
A ventilation rate of 0.6 h-1 (te Biesebeek et al., 2014) for an unspecified room is used. This value reflects the default value for air exchange between the room and the outside environment, while the air exchange between the personal breathing zone and the rest of the room is not accounted for. A Q-factor of 1 is assigned.
Dermal
Dermal exposure to powders can be taken into consideration for mixing the powder with water. Within ConsExpo Web, the dermal – direct product contact – constant rate model is suggested to estimate dermal exposure to powder during loading.
Exposed area
It is assumed that both palms will be dermally exposed during mixing and loading through dust falling on hands or direct contact with the powder. According to the General Fact Sheet, 50% of two hands (=two palms) have a surface of 450 cm2, which will be used as a default here (te Biesebeek et al., 2014). The Q-factor is set to 2 because the underpinning data for the size of the hands is quantitatively rich but the final determination which body parts will be affected during the task is based on expert judgement (see also subsection 4.5).
Contact rate
In the Guidance on the EU Biocidal Products Regulation (BPR), a dermal exposure study for the use of sprinkling/dusting powders to control dust mites has been described (ECHA, 2015a). The subjects in the study applied crack and crevice powders in a kitchen treating skirting boards, shelves and laminate surfaces. The dermal exposure on hands and forearms ranges from 0.4 to 4.18 mg/min with a 75th percentile of 2.83 mg/min. The contact rate for dermal exposure for legs, feet and face ranges from 0.22 to 6.56 mg/min with a 75th percentile of 2.15 mg/min. It is assumed that the values can be adapted for the mixing and loading of DIY powder products. The value for the contact rate of approximately 5.0 mg/min (2.83 + 2.15) is set as a default. The Q-factor is considered to be 1, because the underlying data is rich but collected for the application (not mixing and loading) of biocides in the form of powder.
Release duration
The release duration is assumed to be similar to the exposure duration for inhalation exposure. 3 minutes is set as the default with a Q-factor of 2 because underpinning data is limited.
4.2. Application
Definition of volatile substances
It is important to define whether a substance that has to be evaluated by means of ConsExpo is a volatile or a non- volatile substance. Following the definition provided by Snippe, a volatile substance is a compound with a vapour pressure > 0.1 Pa, non-volatile < 0.01 Pa, and slightly volatile between 0.01 and 0.1 Pa (Snippe et al., 2002).
4.2.1. Spray application
In this Fact Sheet, a few scenarios are described using the spray model, for examples glue spray, putty spray, plaster spray and several remover sprays. These are liquids and suspensions that are applied with the spray mode of application. Here, general parameters for the spray model will be discussed.
Within the context of ConsExpo Web, a spray application is defined as the generation of slowly evaporating or non-volatile substances in droplets that are released from a spray can (Delmaar & Bremmer, 2009; Delmaar & Schuur, 2016). There are three main types of spray applications:
- Aerosol spray cans that use the expansion of a pre-pressurised propellant gas to drive out the aerosol
- Trigger sprays that operate by means of mechanical force from pulling the trigger.
- Pneumatic spraying where the product is applied using an air pressurised device (spray gun) and potentially a compressor. If no compressor is attached, the pressure has to be restored manually by pumping. After pulling the trigger, the product is mixed with the compressed air stream and released in a fine spray.
- Additionally, in recent years, two subgroups of pneumatic spraying became more and more popular in the DIY sector:
- High Volume Low Pressure (HVLP) spray guns require a compressor that provides a constant air flow to distribute a product through the spray gun onto the surface. The difference between this technology and the previously mentioned conventional pneumatic spraying is the lower pressure that is used. Conventional pneumatic spray systems work with a high pressure, which distributes the product as a fine, atomised mist, allowing the user to work on a very intricate level. HVLP systems, however, produce rather large droplets which will result in thicker coats of product on a surface.
- Airless Systems are built similarly to HVLP technology. It requires an electrically run hydraulic pump to move a product from a container through a tube into a high-pressure hose that is connected to a spray gun, which then distributes it across a surface. As the name indicates, no air is involved here; only pressure is utilised to move the product.
The generated droplets comprise inhalable aerosols, but dermal exposure is also expected, as part of the droplets may deposit onto the unprotected skin of the hands and arms. Aerosol spray cans, trigger sprays and pneumatically/airlessly distributed products may contain volatile substances that can evaporate into the air after they have been sprayed upon a surface. Therefore, it is recommended to consider the exposure to such volatile substances as exposure to vapours, so that the inhalation exposure resulting from their evaporation is not neglected.
Inhalation
A major pathway of exposure to spray applications is the inhalation of respirable aerosols generated during the use of aerosol spray cans, trigger sprays and pneumatically/airlessly distributed sprays. Inhalation exposure to these aerosols is driven by a variety of exposure parameters, such as the ventilation rate of the room, the duration of presence of the exposed person in the room during or after spraying, and the way the product is used. Additionally, product-specific characteristics such as the composition, the pressure or the used container (nozzle), are highly relevant to the resulting exposure.
The general exposure scenario for inhalation of substances from spray applications provides interpretations and/or defaults for parameters referring to spray duration, density of non-volatile substances and mass generation rate (i.e., the released mass per unit of time during spraying) for aerosol spray cans, trigger sprays and pneumatically/airlessly distributed sprays.
The exposure to vapour – evaporation – instantaneous release model is used to estimate the exposure to volatile substances from DIY products available on the market as sprays. The Exposure to spray – spraying model is used to estimate inhalation exposure to non-volatile substances when using DIY products as sprays. The parameters of this spray module within ConsExpo Web have been experimentally evaluated in the report by Delmaar & Bremmer (2009). Exposure duration, room volume and ventilation rate are parameters that are not generic. Instead, defaults are specifically derived for each scenario of consumer exposure. The other parameters in the exposure to spray – spraying model are discussed below, describing either the derivation of a generic default value or at least a generic approach to do so. These generic defaults and approaches are consistent with the ConsExpo Web manual (Delmaar & Schuur, 2016), the set of experiments evaluating the critical parameters of the model (Delmaar & Bremmer, 2009), and the General Fact Sheet (te Biesebeek et al., 2014). All consumer exposure scenarios described in the current Fact Sheet to substances in DIY sprays do not consider the ‘spraying toward person’ option, because the intended use is to spray towards surfaces that are to be treated.
Spray duration
‘Spray duration’ is defined here as the net spraying time between start and finish of spraying during the whole event, not counting the time between sprays (Delmaar & Schuur, 2016). A clear definition of ‘spray duration’ is important, because the amount of spray available for inhalation is simulated in ConsExpo Web from the mass generation rate of the spray, the spray duration and ventilation (Delmaar & Schuur, 2016). Default values for spray durations are derived per specific scenario for consumer exposure.
Room height
The default of room height is based on a standard room height of 2.5 m as explained in the General Fact Sheet (te Biesebeek et al., 2014) with a Q-factor of 4 because the underpinning data is quantitatively rich.
Inhalation rate
Spray tasks are considered to be light exercise in the DIY sector. The inhalation rate is therefore set to 1.49 m3/h by default for adults (te Biesebeek et al., 2014).
Mass generation rate of aerosol spray cans
The definition of mass generation rate of sprays is in contrast to that of the Cleaning Product Fact Sheet published in 2006 (Prud’homme de Lodder et al., 2006) where mass generation rate is defined as the average mass released per unit of time over the entire duration of the cleaning task. In the current Cleaning Product Fact Sheet, and consistently in the DIY Products Fact Sheet, the mass generation rate of a spray product is defined as the mass released per unit time of spraying. In the study by Delmaar & Bremmer (2009) such mass generation rates were determined for aerosol spray cans by spraying for 10 seconds and determining the weight loss in the spray can afterwards. To get more insight into the variation of the mass generation rate during the lifetime of the product, the weight loss was measured when the spray container was still full and also when the container was nearly empty (Delmaar & Bremmer, 2009). In these experiments, performed on 17 aerosol spray cans, the mass generation rate ranged between 0.29 and 2.2 g/s. This is consistent with the data from a comparable series of experiments by Tuinman, which show a 75th percentile of 1.2 g/s (Tuinman, 2004; Tuinman, 2007). The default mass generation rate for aerosol spray cans is therefore set at 1.2 g/s. The Q-factor is set to 3, because the underpinning data is quantitatively rich but in a specific exposure scenario, a specific mass generation rate is still preferred over a generic one.
Mass generation rate of trigger sprays
In addition to the aerosol spray cans, Delmaar & Bremmer (2009) experimentally determined mass generation rates for trigger sprays by squeezing 10 times (which approximately takes 6 seconds) and determining the weight loss in the spray can afterwards. The obtained mass generation rates of 6 different trigger sprays ranged between 1.0 and 1.5 g/s. This is consistent with the data from the comparable series of experiments by Tuinman, which show a 75th percentile of 1.6 g/s for trigger sprays (Tuinman, 2004; Tuinman, 2007). The default mass generation rate for trigger sprays is therefore set at 1.6 g/s. The Q-factor is set to 3, because the underpinning data is quantitatively rich but in a specific exposure scenario a specific mass generation rate is still preferred over a generic one.
Please note that the above data on mass generation rates is based on pest control products, cleaning products, cosmetics, paints, lubricants, polishes and cockpit sprays, but not on DIY products. At present, there is no other data available to derive the mass generation rate for DIY products in spray form. The compositions and volume distributions may be significantly different for DIY products; nevertheless, the data will be used as a preliminary source and indication for the dimensions of the values.
Airborne fraction
The airborne fraction is defined as the fraction of the non-volatile material that becomes airborne after spraying as droplets. Default values for the airborne fraction depend on the way in which the product is being used, as well as on the aerosol diameter distribution that has been specified. DIY sprays (glue, putty, plaster, several types of removers) are used to treat surfaces and therefore, are sprayed away from the user onto the surface. Delmaar & Bremmer (2009) have derived a default airborne fraction of 0.2 for such surface spraying activities. This default airborne fraction for surface spraying is derived from data collected for all purpose cleaner spray and flea spray. A specific airborne fraction for DIY sprays, however, was not included the series of experiments by Delmaar & Bremmer (2009). The default surface spraying airborne fraction of 0.2 is included in the calculation of an airborne fraction of DIY sprays that is scaled for the aerosol droplets < 22.5 µm.
Delmaar & Bremmer (2009) state that spray droplet sizes fitted from experimental data to lognormal distributions across the entire range generally proved to be poor. As the smaller aerosols in the distribution are the most critical with respect to inhalation exposure, Delmaar & Bremmer (2009) chose to fit the size distributions in the region of diameters up to 22.5 μm, realising that the fit of the distribution for larger aerosol sizes may not be valid. The airborne fraction for surface spraying is therefore multiplied by a scaling factor that refers to the mass fraction of sprayed droplets < 22.5 µm.
The default aerosol diameter for DYI sprays (see aerosol diameter below) actually refers to aerosol diameter distributions with a median diameter of 15.1 µm and a c.v. of 1.2 for pneumatic sprays and 7.7 µm and a c.v. of 1.9 for trigger sprays. These aerosol diameter distribution parameters are actually fitted to best represent the mass fraction of spray droplets, which are < 22.5 µm in series of experiments performed on spray paints and sprays against crawling insects. In addition, Delmaar & Bremmer (2009) derived a scaling factor of 0.7 for the spray paints and a scaling factor of 0.04 for sprays against crawling insects. The airborne fraction is to be multiplied by these scaling factors (Delmaar & Bremmer, 2009), so that the airborne fractions in this Fact Sheet are: 0.2 × 0.7 = 0.14 for the pneumatic DIY sprays and 0.2 × 0.04 = 0.008 for DIY trigger sprays (See Table 3 below).
The Q-factors are set to 2, because the surface sprays that are evaluated in the experiments of Delmaar & Bremmer (2009) include only a small number of samples and none of them belonged to the DIY sector.
Inhalation cut-off diameter
The inhalation cut-off diameter is defined as the diameter below which the sprayed aerosols can be inhaled and reach the lower areas of the lungs, i.e., the alveolar region (Delmaar & Schuur, 2016). It is only an approximation of the complicated process of deposition of aerosols in the lungs, but in practice, its value is suggested to be set at 10–15 μm (Delmaar & Schuur, 2016). In order to be conservative, the default for inhalation cut-off diameter is set here at 15 µm. The Q-factor is considered to be 3, because the value is specifically but qualitatively derived for the parameter inhalation cut-off diameter.
Density non-volatile
The density of the non-volatile fraction is one of the parameters included in the spray model and is defined here as the density of the aerosol droplets that become airborne. Together with the droplet diameter, the aerosol density determines the time that the aerosol droplet is airborne and therefore available for inhalation. Many non-volatile ingredients in DIY products are made of (very) large organic substances with densities between 1.0 and 1.5 g/cm3. The density of salts generally varies between 1.5 and 3.0 g/cm3. For a complex mixture of (organic) substances, the default density is set at 1.8 g/cm3. The Q-factor is set to 3, because density is a physicochemical property that is evident for most substances, but it is presented here on a generic level (Table 4).
Table 4
Default values for density non-volatile substances (Prud’homme de Lodder et al., 2006a).
Aerosol diameter
The aerosol diameter of the sprayed droplets is an important parameter when estimating the exposure. Smaller drops fall at a lower speed and stay in the air longer. Large droplets will quickly disappear from the air after being formed. As an indication, the falling time of droplets with a diameter of 100 µm from a height of 3 metres is calculated to be 11 sec, and for droplets of 10 µm it is calculated to be 17 minutes (Biocides Steering Group, 1998). If a larger droplet is sprayed, part of the aerosol cloud will consist of finer droplets, which will stay in the air longer, as a result of edge effects around the nozzle and the ‘bounce back’ effect due to spraying onto a surface.
Measurements provided by Delmaar & Bremmer (2009) and Tuinman (2007) regarding the aerosol diameter distribution of various spray products lead to the default values listed in Table 5.
At present, there is no information available on the aerosol diameter distributions of DIY products. Nevertheless, as DIY sprays are exclusively used for surface spraying, it is assumed that results referring to similarly used spray products can be considered to be reasonable estimates for the DIY sector, too. Following this paradigm, the default for aerosol spray cans is set at a lognormal distribution with a 15.1 µm mass median diameter and c.v. of 1.2 (default for paint containing spray cans fitted to best represent the mass fraction of droplets < 22.5 µm). Furthermore, the default aerosol diameter distribution for the use of trigger sprays is a lognormal distribution with a mass median diameter of 7.7 µm and a c.v. of 1.9 that was originally fitted to best represent the mass fraction of droplets < 22.5 µm in sprays against crawling insects. The Q-factors are set to 1.
Table 5
Defaults for aerosol diameter distribution (median [µm] and coefficient of variation) (Delmaar & Bremmer, 2009).
Oral non-respirable material exposure
Non-respirable oral exposure is expected from material in aerosols with a diameter larger than the inhalation cut-off diameter. Aerosols of this size are deposited in the higher regions of the respiratory tract, so that they are taken up orally. ConsExpo offers the option ‘include oral non-respirable material exposure’. If this option is checked, ConsExpo adds an oral route model to the exposure scenario and accounts for the non-respirable fraction of the inhaled spray. By default, the option is not ‘included’ for DIY sprays, because the larger aerosols are mostly prone to deposit on the surface at which the spray is directed.
Inhalation of volatiles
The inhalation exposure to volatile substances in cleaning sprays is estimated using the inhalation – exposure to vapour – instantaneous release model. The defaults for the parameters exposure duration, room volume, ventilation and inhalation rate described for non-volatiles in sprays (see above) also apply to volatile substances.
Dermal
In this general scenario of exposure to spray applications that are directed at surfaces, the ConsExpo dermal – direct product contact – constant rate model is used to calculate the dermal exposure. The generic exposure scenario for such dermal exposure explains the interpretation of contact rate and release duration. Defaults are derived for contact rate only.
Contact rate for aerosol spray cans
ECHA (2015a) provides data for consumer spray products available as pre-pressurised aerosol spray cans and hand-held trigger sprays, e.g., the consumer product spraying and dusting model developed by the UK Health Safety Laboratory (HSL) in 2001. This non-professional surface spraying model for indoor surfaces describes the use of pre-pressurised aerosol spray cans, e.g., for shelves and horizontal/vertical laminate surfaces. The model calculates a 75th percentile of 64.7 mg/min for dermal exposure on hands and forearms, while for legs/feet and face a 75th percentile of 35.7 mg/min is provided, so that the total contact rate for the use of aerosol spray cans is roughly 100 mg/min. Hence, the default for contact rate – aerosol spray cans is set at 100 mg/min. The Q-factor is 3, because the underpinning data is quantitatively rich but not specifically collected for DIY products available in aerosol spray cans.
Contact rate for trigger sprays
For the use of hand-held trigger sprays, ECHA (2015a) describes a non-professional surface spraying model for spraying indoors in small rooms, i.e., dining chairs and carpets. The 75th percentile for contact rate after dermal exposure on hands and forearms is 36.1 mg/min, while for legs/feet and face, it is 9.7 mg/min, yielding a total contact rate for trigger sprays of roughly 46 mg/min. Hence, the default for contact rate for trigger sprays is set at 46 mg/min with a Q-factor of 3. The Q-factor is 3 because the underpinning data is quantitatively rich but not specifically collected for DIY products available as trigger sprays.
Contact rate for pneumatic spraying
A contact rate regarding the use of a pneumatic spray system is not described in the Cleaning Products Fact Sheet. Therefore, the following description is provided.
In the TNsG’s (European Commission, 2002) ‘Consumer product spraying and dusting’, a surface spraying model is stated in which the consumer uses an electric powered sprayer outdoors for spraying all types of fence with a wood preservative. The dermal exposure on hands and forearms ranges from 32.4 to 144 mg/min with a 75th percentile of 72.6 mg/min. The dermal contact rate for legs, feet and face ranges from 13.4 to 84 mg/min with a 75th percentile of 39.9 mg/min. Based on the data above, the default value for the contact rate during pneumatic spraying for the total dermal exposure is set at 110 mg/min with a Q-factor of 3 because underpinning data is quantitatively rich but not specifically collected for indoor use of DIY products (Bremmer & van Engelen, 2007).
Release duration
Dermal exposure is expected to occur both during the actual spraying event and the time between spray events. The release duration should therefore be equal to the intermittent spray duration (total duration of the whole spraying task) in case spraying is not continuous.
4.2.2. Evaporation pattern of adhesives
Inhalation
The evaporation pattern of adhesives is different from that of most other DIY products. In contrast to paints, for instance, the surface from which chemicals from adhesives can evaporate is not constantly ‘open’. Adhesives are implicitly used to connect parts. This means that the adhesive is covered with the part that is to be connected. The time during which there actually is a surface–air situation is described as the ‘open time’ of glue. This open time may range from a few seconds to several minutes. The duration of this open time depends on the hardening process and thus on the type of glue. Solvent-based adhesives have relatively short open times, in contrast to (most) water-based adhesives, due to a relatively higher evaporation rate. Polyurethane-based glues are covered after application to prevent reaction with moisture, which is not desirable for a good end result.
The evaporation pattern of adhesives starts with a relatively high temporal evaporation rate (during open time), which is then followed by a relatively slow constant evaporation rate (when the surface is covered). Experimental data from solvent-based glue products shows that the starting emission rate is of the magnitude of 0.4 g/m2 per second. After covering the applied product, the vapour concentration will rapidly drop below the odour (smell) detection limit (in the order of 10–20 ppm for solvents) (personal communication with Vereniging Nederlandse Lijmindustrie (VNL) conducted by RIVM during the preparation phase for the 2007 DIY Products Fact Sheet).
Currently, there is no evaporation model in ConsExpo which can describe this two-phased evaporation pattern of adhesives. For this reason, the exposure to vapour – evaporation – release area mode: increasing model is used for relatively small tasks (and amounts). The time during which evaporation takes place is set to be equal to the exposure duration, which is in fact a conservative approach.
Relevant parameters for the exposure to vapour – evaporation – release area mode: increasing model besides the general parameters (exposure duration, product amount, weight fraction of the substance, room volume and ventilation rate) are:
- Release area: The total surface area the product is applied to.
- Application duration: The time period during which the product is applied.
- Temperature: The room temperature prevailing during exposure.
- Molecular weight and vapour pressure: The physicochemical properties of the substance in question.
- Mass transfer coefficient: The rate that describes the transfer of the substance in question between the product’s surface and the air. For further explanations, see subsection 4.1.1.
However, this approach is not considered appropriate when larger gluing tasks are considered. A large task must be divided into segments when the total time required to apply the glue and connect the parts exceeds the open time of glue (see above). This will result in repeated ‘peak’ exposures during the task. Examples of such large tasks are gluing parquet, tiles and carpets. The exposure to vapour –evaporation – release area mode: constant model is used for repeated ‘peak’ exposures within a task. The relevant parameters for this model are largely similar to those mentioned above. One exception is the emission duration, which is necessary instead of the application duration.
- Emission duration: The time period during which the substance is released from the product.
Because (simultaneous) evaporation from the total surface area during a large project is not realistic (laying carpet, gluing parquet etc.), an alternative description of exposure is required to integrate the repeated exposures during these large tasks. The release area is set to be equal to the surface area one can treat per segment. It is assumed that an individual treats 1 m2 per segment (4 m2 for carpet gluing). After that, the surface is covered, and the exposure is considered negligible compared with the surface to be treated next. These steps are repeated until the task is completed. It is assumed that the inhalation exposure is described by evaporation of the total amount, rather than the adjusted amount, from a constant surface area, i.e., 1 m2. The exposure to vapour – evaporation – release area mode: constant model is used. This simplification of the model is necessary, to overcome the problem of depletion of the source. The emission duration and the exposure duration are set to be equal during these tasks because considering the interval approach, a source depletion of the segments is not expected.
4.2.3. Dermal exposure
Describing the dermal exposure to certain DIY products can be troublesome. Because glue spills or other DIY products on hands can complicate the task for the user, he/she may tend to clean or wipe his/her hands. The result of this behaviour is that the exposure increases from the moment the user starts, decreases when the hands are cleaned, and increases again when the task is continued. When the product contains components that are not absorbed easily through the skin, lower internal exposure is expected; but when a component is absorbed rather easily, internal exposure is evident. However, for many components the dermal absorption rate is unknown.
Currently, there is no dermal exposure model available to describe this fluctuation in exposure. ConsExpo provides two models, the dermal – direct product contact – instant application model and the dermal – direct product contact – constant rate model, both of which can be used to describe this kind of exposure. To illustrate the difference between the two models, consider a total dermal load (e.g., X) that a subject is exposed to on completion of the task. The instant application model assumes that the subject is exposed instantly to X amount of the product which remains on the skin during the task. This results in an overestimation of the exposure. For large tasks, the dermal load may rise up to grams. Being exposed instantly to such an amount is not realistic. The constant rate model describes a more gradual increase in the dermal load over time, up to the amount X. The contact rate is determined by dividing the total amount by the time of use. Information on the release duration is required. In total, this is a conservative approach for products that contain volatile substances because it neglects that a part of the substance evaporates over time and is therefore not available for dermal exposure anymore. Another point is that glues are designed to harden in a certain (mostly short) period of time, which also reduces dermal exposure. Furthermore, during the use of two-component products, a chemical reaction takes place when both components are mixed. During this process, part of the substance in question may be consumed by the reaction, which would also lead to lower exposure values. However, this model seems to describe a somewhat more realistic scenario because it is not known to what extent a subject is exposed during the task. In other words, the constant rate model describes the pattern of exposure better than the instant application model does, although we do not know the pattern exactly.
In this Fact Sheet, it is recommended to apply the dermal – direct product contact – instant application model when dermal exposure is expected to be low or the task relatively small. In such cases, a subject will not clean his/her hands during the task. Then again, for relatively large tasks where large spills can be expected, the dermal – direct product contact – constant rate model is applied because this provided a more realistic scenario for the subject’s behaviour in view of dermal exposure.
Dermal – direct product contact – instant application
Dermal exposure: product amount
Dermal exposure while using DIY products is often caused by spills. The product amount which actually contacts the skin directly depends on the consumer’s behaviour, the DIY task, the product itself and the total amount used. To obtain more insight into the amount spilled during a task, a short experiment was conducted (see Annex II, A.2). During the experiment it was established that a drop of glue weighs approximately 50 mg. Spreading a small amount of glue twice, using one finger which led to exposures of 30 mg and 90 mg. When the palm of a hand is fully covered with glue, it was estimated that the product amount contacting the skin is 1 g. When such an amount is spilled, the subject may not be able to proceed without cleaning their hand first.
In an update of the Paint Products Fact Sheet (2007), the relationship between the manner of painting (overhead, downward, or painting to the side at chest height) and the spilled amount is described (Bremmer & van Engelen, 2007). The amount of paint spilled also depends heavily on the type of paint, surface area and its accessibility. For several paints it was described that the amount spilled equalled on average up to 0.2% of the total amount required. This figure ranged from 0.09% to 0.56%. The product amounts ranged from 250 g to 1,800 g.
In contrast to paint, there is a wider range of product amounts in DIY products – in some cases the amount can add up to several kilograms. Furthermore, dermal exposure to paint is different from dermal exposure to specific DIY products, such as glue or sealant, which might hamper the user from completing the task. The user will then have to clean their hands before continuing with the task. In those situations, the relationship between product amount and amount spilled is different compared to paint. Nevertheless, the described relationship can provide useful estimates of spilled amounts. A general default value could not be derived for DIY products. See the product categories for the default values for dermal product amounts.
Dermal – direct product contact – constant rate
Contact rate
The dermal contact rate is required when the constant rate model is advised. A dermal contact rate has not been determined for DIY products so far. For several paints, contact rates were determined under various circumstances, summarised in the TNsG (European Commission, 2002). Four exposure models are described for consumer painting. Values (75th percentiles) were found to range from 17 to 186 mg/min, with most values around 50 mg/min. In the Paint Products Fact Sheet (2007), the manner of painting affects the dermal contact rate. Three default values for the contact rate were established; overhead painting with low viscosity products, overhead painting with ‘normal’ viscosity products, and downward painting or painting at chest heigh. These defaults were 120 mg/min, 60 mg/min, and 30 mg/min, respectively. It is assumed that the use of DIY products can best be compared with either overhead painting with products of ‘normal’ viscosity or with downward or chest-height painting tasks.
It is acknowledged that no data is available on DIY products. Thus, the comparison with paints is made qualitatively rather than quantitatively. A contact rate of 50 mg/min seems low (equal to one drop of glue spilled per minute; see Annex II, A.2), but it may add up to several grams when a task is conducted for several hours. In that case, spills from DIY products may hamper a subject from performing a task, causing subjects to clean their hands more often. Therefore, for large tasks a default value of 30 mg/min is set, with a Q-factor of 1.
4.2.4. Generic exposure scenario – application of diluted products
As described in subsection 4.1.2, several DIY products require dilution (with water) prior to use. These products mainly involve remover products in the DIY segment. During application, dermal contact with the product is highly probable. Furthermore, diluting a product in hot water may increase the evaporation process and the subsequent inhalation of volatile substances.
Inhalation
Inhalation of water-diluted products is calculated using the ConsExpo inhalation –exposure to vapour – evaporation model (Delmaar & Schuur, 2016). In order to follow the generic exposure scenario for product dilution with water, some interpretation and defaults are required for the parameters product amount (dermal) and dilution times.
Dilution (times)
For products that are diluted with water, it is necessary to correct for dilution in order to correctly simulate the evaporation of substances (Delmaar & Schuur, 2016). Such corrections are done with a dilution factor that was presented as a new feature in the ConsExpo Web tool in 2018. The equation to calculate the dilution times is derived as:
Dilution: dilution as ‘times’; Asolvent: amount (mass) of solvent (g); Aproduct: amount of pure product (g).
Thus, the dilution is calculated as the inverse of the weight of the amount (mass) of pure product used divided by the total mass of the diluted product (i.e., the sum of the pure product and the solvent).
For example, consider liquid rust remover that has to be diluted in water prior to use. 200 ml rust remover has to be mixed with 1800 ml water, both with a density of 1 g/ml. The amount of solution used represents the sum of the solvent amount and the product amount, which in the example is 1800 g + 200 g = 2000 g. The weight fraction of the product amount in the amount of solution used is then 200 g / 2000 g = 0.1. The number of dilution times is the inverse of this weight fraction, 1/0.1 = 10 times.
Dermal
If the dermal – direct product contact – instant application model is used to calculate dermal exposure from diluted products, the following considerations for the product amount should be taken into account (mainly for smaller applications).
Product amount
The default product amount on the skin is calculated from the concentration of the product following dilution in a container, such as a bucket. This concentration is calculated by dividing the amount of product (Aproduct) inserted into the container by the volume of water in the container (lwater in mixing vessel). The volume of water that comes into contact with the skin (lwater on skin) is derived by means of the surface area of the exposed skin multiplied by the layer thickness of liquid film (0.01 cm), which is taken from the Guidance on Information Requirements and Chemical Safety Assessment Chapter R.15: Consumer exposure assessment (ECHA, 2016), where a general layer thickness for liquid runoffs is set at 0.01 cm. The product amount that comes into contact with the skin is then calculated by multiplying the concentration of the product in the water by the volume of water that comes into contact with the skin, calculated as follows:
The Q-factor for such a calculated parameter value is 2 at most because that is the lowest Q-factor of the variables from which product amount is calculated (layer thickness).
Please note that if a powder product is mixed with just a small amount of water resulting in a more paste-like final product, this approach is not feasible. In these cases, the dermal load will be determined individually.
Dilution
The dilution for estimating dermal exposure will be presented as an additional parameter in the new features of ConsExpo Web. It refers to the number of times the product is diluted into a solvent, which is most often water, and can be derived using the same approach as described above for estimating inhalation exposure. In the current Fact Sheet, dilution times for dermal exposure are not explicitly presented. All external dermal exposure estimations are either done with the dermal –direct product contact – instant application model or the dermal – direct product contact – constant rate model, where dilution is not a parameter. However, the current Fact Sheet does describe consumer exposure scenarios that include dermal exposure from applications of diluted products. In these scenarios, dilution is nonetheless accounted for by calculating the product amount that is in contact with the skin by multiplying the concentration of the product in the water by the volume of water that is on the skin of the consumer (see above). Please note that it is necessary to correct substance properties such as diffusion and permeability coefficients for the properties of water upon contact with diluted products when using dermal exposure models other than those prescribed in the current Fact Sheet, e.g., diffusion models.
4.3. Post-application
Post-application exposure is interpreted across the Fact Sheets as exposure to a product while the exposed person is not actively performing the task the product is intended for. In the case of DIY-products the most common post application activity is cleaning up. Additional dermal exposure (for instance, through contact with product-soaked residues) and onward inhalation exposure, because the consumer stays in the same room after using the product, possibly occur during cleaning.
The clean-up phase may include several steps, such as the gathering of residues (e.g., detached wallpaper), removal of product from surfaces accidentally treated (e.g., inaccurate spray application), cleaning of used tools/utensils (e.g., with a solvent) or cleaning dirt from the work area resulting from the conducted task (e.g., rust/remover mix after removing rust from an object). This process mainly affects the default for the exposure duration, which has to be expanded depending on the extent of the cleaning task in order to assess the exposure sufficiently conservatively. The dimension of the cleaning task is not generic and therefore explained in the particular exposure scenarios.
4.4. User population
The defaults described in this Fact Sheet are derived for consumers, not for professional use of the products concerned, for example on constructions sites. Therefore, only products are considered that are available on the market for the average consumer.
Non-professional users of DIY products comprise both men and women. The average size of body parts for adults, their body weight and their inhalation rates are taken from the defaults provided in the General Fact Sheet (te Biesebeek et al., 2014). The inhalation rate depends on the task conducted and the related physical effort the user has to exert. It is therefore not generic and needs to be determined individually for the particular exposure scenarios.
Body weight
The body weight of the adult user is set at 68.8 kg as a default with a Q-factor of 4 (te Biesebeek et al., 2014). Please note that in the regulatory context, it may be necessary to adjust this default according to the obligations of a specific regulation (e.g., in the REACh context, the default for the body weight of an adult user is considered to be 60 kg).
Surface areas
It is most likely that individuals will be dermally exposed to their hands while working with DIY products, where both intentional and accidental contact may occur. The surface area for both hands is set at 900 cm2 by default (te Biesebeek et al., 2014), whereas sometimes only one hand or one palm will be taken as an exposure area. These surface areas relate to the total surface area by a factor 0.5 or 0.25, respectively. Fingertips are quite often used during DIY tasks, for example to smooth joints made from sealants. Their surface area is set at 15 cm2 per fingertip (see subsection 4.1.1).
4.5. Addendum regarding the derivation of Q-factors
During the work on the Fact Sheets, a special case was identified when it comes to the quantification of the Q-factor. This case is characterised by the following conditions:
- The value for a parameter is based on a sufficient and quantitatively rich dataset
- An assumption, based on expert judgement is made to derive the final default
One example for such a case is the exposed dermal area. For one thing, we have a profound dataset regarding the sizes of different skin surface areas (e.g., for the hands, upper body etc.) from the General Fact Sheet (te Biesebeek et al., 2014) which would result in the assignment of a Q-factor of 3. Then again, the estimation of the extent of the affected area is in most cases expert judgement without underpinning data, which would result in a Q-factor of 1.
In these cases, it is proposed to assign a Q-factor that represents the quality of the derived default value in the context of the individual exposure scenario in order to avoid the implication of an unjustified quality level.
In practice, the Q-factor is set to 2 if expert judgement is combined with profound data in order to derive the final default because of the resulting uncertainty that correlates with subjective assumptions.
- Generic scenarios and models for Do-It-Yourself products - Do-It-Yourself Produc...Generic scenarios and models for Do-It-Yourself products - Do-It-Yourself Products Fact Sheet: Default parameters for estimating consumer exposure – Updated version 2022
- Homo sapiens TNF superfamily member 10 (TNFSF10), transcript variant 3, mRNAHomo sapiens TNF superfamily member 10 (TNFSF10), transcript variant 3, mRNAgi|1676318051|ref|NM_001190943.2|Nucleotide
- Homo sapiens TNF superfamily member 10 (TNFSF10), transcript variant 4, non-codi...Homo sapiens TNF superfamily member 10 (TNFSF10), transcript variant 4, non-coding RNAgi|1701108590|ref|NR_033994.2|Nucleotide
Your browsing activity is empty.
Activity recording is turned off.
See more...