NCBI Bookshelf. A service of the National Library of Medicine, National Institutes of Health.
National Research Council (US) Chemical Sciences Roundtable. The Role of the Chemical Sciences in Finding Alternatives to Critical Resources: A Workshop Summary. Washington (DC): National Academies Press (US); 2012.
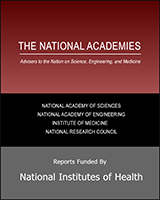
The Role of the Chemical Sciences in Finding Alternatives to Critical Resources: A Workshop Summary.
Show detailsThe amount of energy that can be stored by a battery depends on the specific battery technology being used and on the amount of material in the battery. For large-scale battery applications, therefore, such as storage of energy for grid-scale applications, the availability of battery materials is critical. However, other factors are also important, such as processing costs, battery assembly, and the cost of secondary components.
The integration of batteries into the energy supply system on a large scale is ultimately a systems problem that involves processing, structure, properties, and performance of materials with considerations of cost, policy, and environmental impacts. Furthermore, the system is so large that it will take at least a decade or two for a new technology to mature and have a significant impact.
CRITICAL MATERIALS FOR BULK ENERGY STORAGE
“Grid-scale energy storage is considered to be the holy grail for electricity storage,” said David Bradwell. “Whether it’s supporting conventional resources such as nuclear, solar, or wind, there is a great demand to have storage on the grid in order to balance electricity supply and demand.”
The current electrical grid supplies power in real time in response to demand. When demand increases, output must increase. As demand changes throughout the day, generators ramp up and down to meet that demand. When supply and demand become decoupled, the result can be catastrophic failure, as was the case with the 2003 blackout that affected millions of people in the northeastern United States. When a few generators went down, there was no buffer in the system to account for the sudden decrease in supply.
Energy storage can act as a buffer on the grid. It can smooth out the power from intermittent renewables, such as solar and wind, and it can match the supply from generators on the grid powered by nuclear energy, natural gas, and coal.
Power, Energy, and Material Constraints
There are two important considerations for energy storage: power and energy. Power, Bradwell explained, is a surface area effect. To produce more power from solar cells requires a larger surface area of photovoltaics to capture more light. There are other ways to capture more light without changing surface area, such as with concentrating mirrors or changing the thickness of the semiconductor layers, and those approaches to optimizing the use of a given amount of surface area can have a significant impact on the amount of active material required to produce a given amount of power. New materials, such as cadmium telluride, also play a role in the amount of material required to produce a given amount of power.
Energy is a function of volume. Battery storage capacity is directly related to the amount of active material used. “If you want to store a lot of energy in a battery, you need a lot of active material,” said Bradwell. “There is no way to get around it. There is no opportunity for optimizing the amount of material used with battery storage.”
As a result of this basic limitation, it is important when thinking about battery storage on the scale needed for energy grid applications to consider the various constraints regarding battery materials. A major constraint is the abundance of a given material on Earth, as described in previous talks. For example, iridium might prove to be a great battery material, but its low abundance rules it out as a real candidate for large-scale battery applications. The same holds true for tellurium, for which some phenomenal battery chemistries exist. On the other hand, lithium’s crustal abundance is quite high, as is that of magnesium and antimony, two materials that also hold promise in battery technology.
The scale of production, the reserve base, and the cost also can be limitations. Focusing on three specific chemistries—sodium sulfur, lead oxide or lead acid, and lithium iron phosphate—Bradwell explained that it is important to look not just at raw material costs, but at total battery costs. The elemental cost of sodium sulfur is tiny, less than $0.10/kilowatt-hour (kWh), whereas that for lead acid is much higher, between $10 and $30/kWh, and lithium iron phosphate costs come in around $1/kWh. Looking at the total cost of the battery paints a different picture. Sodium sulfur batteries cost $300 to $500/kWh, while a lead acid battery costs between $100 and $300 kWh and a lithium iron phosphate battery costs between $300 and $1,000/kWh (Wadia et al., 2011). The Advanced Research Projects Agency-Energy goal is $100/kWh (Figure 6-1).

FIGURE 6-1
Costs of raw electrode material affect final battery costs. SOURCE: Adapted from Wadia et al. (2011, p. 1596, in Bradwell 2011a).
Electrode material costs are not the only driver of battery cost. Processing costs to produce high-purity starting materials, battery assembly, and the expense of secondary components such as the electrolyte, current collector, current lead, housing, and safety features can be important cost factors. High-purity sodium and lithium iron phosphate are expensive to produce. In contrast, if the cost of lithium were to increase by a factor of 10, it would have little effect on the price of a lithium battery, said Bradwell.
Supply issues can be a concern. The United States has substantial reserves of lithium brines, and China, Canada, Brazil, and Australia have reserves of lithium carbonate. Bolivia has the largest resources of lithium brines, but their profitability is uncertain. There are strategic concerns about lithium supplies, but lithium ranks at the low end of supply risk in terms of minable reserves.
“Cost and natural abundance alone do not appear to be major limitations for lithium,” said Bradwell. “There are opportunities for better understanding the system and the processing costs and materials. In the academic world, people get very excited about making something that works and works well, but for these broad-scale applications, we should be thinking about assembly, processing, manufacturability of the system, and scalability.” He added that there is an opportunity for possible collaboration between those who are inventing the chemistries and batteries and the experts who could ultimately help build and deploy these systems.
New approaches to making batteries can use lower-cost processes and assembly methods. In addition, it may be possible to develop batteries that use lower-purity, and therefore lower-cost, materials. There may also be ways of improving lithium extraction processes to enable the use of lower-quality ores or brines.
Grid-Scale Storage
While the conventional metrics for battery storage are energy density and power density, the key metrics for grid-based storage are cost, lifespan, and energy efficiency, said Bradwell. Looking at energy density, lithium and sodium sulfur batteries score well, while pumped hydroelectric power compares poorly. However, for grid storage, pumped hydro dominates (Figure 6-2) because of its low cost to deploy, long lifespan, and its greater than 70 percent efficiency. Bradwell noted that there is a nice relationship between the cost of a technology and its deployed capacity. At a cost of between $100 and $200/kWh, adoption takes off.

FIGURE 6-2
Grid-based energy storage technologies have different energy densities and installed capacities. SOURCES: ESA (2010); Bradwell (2011b).
Other promising battery technologies include flow batteries, magnesium batteries, and zinc manganese oxide batteries. Lead acid batteries, a technology that has been around for a long time, also have the potential to contribute to grid-based storage.
Challenges must be solved for all of these new battery chemistries. Dendrite formation, a particular problem with zinc batteries, occurs when metal is deposited on a battery electrode, extends across the electrode, and eventually shorts the battery. Electrode cracking and deterioration is still a challenge that arises when material intercalates within the structure of the electrode. This is a major mechanism for electrode failure in batteries. Nanostructured materials may solve this problem, but these materials are more expensive to use.
Interfacial film growth caused by the slow reaction with electrolytes is another major challenge. The electrolyte in a lithium battery is actually unstable. It reacts with the electrode and forms a layer on the surface of the electrode that grows slowly. The layer is necessary for battery performance, but it should be stable. As the layer grows, it increases the battery’s impedance and lowers performance.
Flow batteries are an interesting technology in which energy is stored in an electrolyte that is pumped across a membrane surface. Fuel cells are getting increasing attention, but efficiency is the big challenge there. Lithium battery efficiencies reach 90 to 95 percent, while the round-trip efficiency on a fuel cell is typically closer to 50 percent. What is encouraging, said Bradwell, is that most of the new approaches that researchers are pursuing use Earth-abundant materials such as zinc, magnesium, lithium, manganese, sodium, and lead. Very few of the new chemistries use resource-constrained materials.
In his work, Bradwell took inspiration from the metals industry’s experience that prices drop as production increases and that prices drop more when materials are processed as liquids. “Both iron and aluminum are produced as liquid metals [that are] handled and processed in a continuous manner, which also keeps the costs low,” said Bradwell. “In particular, the aluminum smelter was the inspiration for the liquid metal battery project.”
An aluminum smelter is a huge electrolysis machine that works as follows: aluminum oxide is poured into a layer of molten cryolite, which at 960°C is so corrosive that it dissolves aluminum oxide and dissociates it into aluminum ions and oxygen ions. A 700-milliampere/cm2, 4-volt (V) current is passed from cathode to anode, which oxidizes aluminum ions to liquid aluminum. This pools underneath the electrolyte and reduces oxygen to carbon dioxide, which is vented to the atmosphere. Though a simple reaction in theory, it proved to be difficult to carry out in practice. Before this process was developed, aluminum was more expensive than gold.
In essence, Bradwell explained, an aluminum smelter is half of a battery that cannot be recharged because it generates a gaseous product that cannot be reclaimed. The solution was to replace this gaseous component with another liquid metal. In the liquid metal battery, an electropositive liquid metal is separated from an electronegative metal by a liquid electrolyte. The three liquids self-segregate based on contiguous immiscibility between the metal and electrolyte layers. The battery operates at high temperature, though less than that of an aluminum smelter, and uses low cost materials. The aluminum industry’s experience suggests that the electrodes will have a 5- to 10-year lifespan before they need refurbishing.
The first generation battery he and his collaborators built used liquid magnesium and antimony as the two electrodes. At low current densities, this battery was 74 percent efficient, with a coulombic efficiency—a measure of self-discharge—of 99.7 percent per cycle. The voltage of this initial battery was low, only 0.5 V compared to 3.5 V for a lithium-ion battery. Fundamental research and chemical development efforts have raised the output to 0.9 V, which is still low but sufficiently high to continue work on this system, and coulombic efficiency has increased to greater than 99.9 percent. Projected costs for such a battery would be less than $100/kWh. Bradwell acknowledged that a significant amount of work needs to be done on failure mechanisms, chemistry optimization, scale-up, and systems engineering.
Semiconductor Recycling
During the course of developing the liquid metal battery, Bradwell and his collaborators came up with a new method for recycling or reprocessing intermetallic compounds such as tellurium. While running electrochemical experiments on molten zinc chloride, the researchers noted that, under an applied potential, zinc would start depositing on one of the electrodes, with the corresponding release of chlorine gas. This is standard electrochemistry and not a surprise, but when they added zinc telluride to the system, experimental data showed that tellurium was dissolving as an anion, a totally unexpected finding because metals usually dissolve as cations.
This finding prompted Bradwell and his colleagues to develop a system for producing zinc and tellurium from zinc telluride, which while interesting is not relevant to anything practical because zinc telluride is not widely used. Cadmium telluride is, however, so the researchers created a method for taking cadmium telluride manufacturing scrap and converting it into high-purity cadmium and tellurium. This is not a technology relevant to batteries, he said in closing, but it could play a role in addressing concerns about tellurium supplies.
ALTERNATIVE MATERIALS FOR ENERGY SYSTEMS
Energy policy, said Jay Whitacre, can be represented as a polyhedron that connects characteristics subject to research and development such as structure, processing, properties, and performance with considerations of cost, policy, and environmental impact (Figure 6-3). If the field does not address issues of cost, policy, and environmental impact as part of its research on characteristics, the impacts of new energy technologies will be small.

FIGURE 6-3
Factors in energy technology engineering can be envisioned as occupying the corners of a polyhedron. SOURCE: Whitacre (2011).
When considering whether a new technology has market potential, Whitacre makes two assumptions specific to materials-intensive energy technologies. The first assumption is that cost is everything. To have an impact, projects must be huge, particularly given that the goal is to alter the way that the world consumes or distributes power and energy. This is a tremendous materials challenge, and not just with the cost of the materials. Other costs include the capital to manufacture these new technologies, the cost of production throughput, operational expenditures, transportation costs, and the expense of integrating new supply. Developers of these technologies also need to make a profit and return on their investments, which adds to a technology’s costs. “We’re not just doing this as a philanthropic exercise,” said Whitacre. “You can’t change the world with technology unless those technologies are profit-bearing.”
The second assumption is that a systems-level perspective is the only one that matters for energy technologies. “The economy and policy makers only care about the macro implications of energy technologies,” said Whitacre. “At the end of the day, they have to decide what to fund and what to give emphasis to if they are making policies that will affect the implementation of some technologies over others.” As a result, black-boxing is critical—think of a technology in terms of a box that either produces electrons or stores and releases them. Then, determine how that box will fit in the existing system, how it will function in the system’s environment, how it can improve the system in which the box sits, and how the box affects the cost, performance, and lifetime of the system.
Whitacre added that the movement of materials through the supply chain and value chain also should be examined this way—an analysis should determine what materials move into the box and what materials move out of the box. It is necessary, he said, to determine how this material flow affects the manufacturing cycle and disposal cycle. The conclusion from this assumption is that trade issues are crucial and should inform even fundamental research on technologies. It is important, too, to keep a 10- to 20-year timeframe in mind because that is how long it will take a technology being developed today to make a significant impact on the system.
Lithium-Ion Batteries
There is plenty of lithium in the world. According to the U.S. Geological Survey, there are some 32.5 million metric tons of lithium reserves worldwide, enough to make 32.5 billion vehicles equipped with today’s lithium-ion batteries. Today, developed reserves are dominated by Chile and China, and the market is currently flooded with supply. Battery-quality lithium carbonate costs less than $5/kg, and the other materials in a lithium-ion battery—cobalt oxide, manganese oxide, copper, and aluminum, among others—are also relatively inexpensive and plentiful.
What is expensive is the system that all of these materials fit into to make a battery (Figure 6-4). The system includes current collectors, separators, and the electrodes themselves, which are active materials and quite thin at less than 100 microns per anode or cathode for high-powered devices. In addition, ancillary support such thin electrodes, and in fact the thinner the electrode, the more ancillary material is needed to support it.

FIGURE 6-4
A lithiumlithium-ion cell has multiple components. SOURCE: HowStuffWorks, circa 2006, Bryan Christie Design.
There are trade-offs involving costs. Power costs more per unit of active material, but power is also worth more in many applications. More complex batteries may perform better and command a better price, but more complexity can create yield problems if cell-to-cell consistency is critical for performance.
An examination of the bill of materials for a generic plug-in hybrid vehicle lithium-ion battery reveals that, of the $300 to $400/kWh cost of this battery, all of the materials cost about $100/kWh. Even if the lithium cathode cost went to $0, the next-generation automobile lithium-ion battery would still cost over $400/kWh. An assessment by the Boston Consulting Group (BCG, 2010) came to a similar conclusion, finding that materials represent about 12 percent of the cost of a lithium-ion battery supplied to an automobile manufacturer. Depreciation, research and development, and parts each accounted for a larger percentage of the cost of the battery.
The most expensive part of a lithium-ion battery is actually the electrolyte. Manufacturing costs associated with the organic solvent electrolyte are high, and its ionic conductivity is relatively low compared to aqueous electrolytes. Lower ionic conductivity means that the electrodes must be thinner, which in turn boosts the costs of the ancillary materials needed to support thin electrodes. A quick sensitivity study shows that batteries become cheaper as electrodes get thicker, but this demands a higher-conductivity electrolyte and clever electrode structural engineering. In addition, the rate capability goes down.
The bottom line is that adoption of lithium-ion battery technology is not constrained by materials. Rather it is constrained by the way the materials function and the complexity of the device itself.
Bulk Stationary Storage
The development of bulk stationary storage devices is critical to the next-generation grid and large-scale use of renewable energy sources. A handful of companies are making progress not through the use of innovative chemistry but through clever engineering and by filling specific niches where higher prices are justified. A technology developed by Xtreme, for example, is being installed on Maui, which has a major problem with frequency regulation because of all the wind power being generated there. Power developer AES Corporation is installing A123 Systems’s batteries at what Whitacre called extreme pain points—places where transmission problems are severe enough to justify the high cost of these systems.
Pumped hydro, a well-established technology, is not universally cheap, Whitacre noted. It requires a vertical gradient and plenty of cheap water, and it is not very energy dense. The real competitors for bulk storage are small natural gas turbines used for peak-hour demands and renewable leveling. They cost about $750/kW installed, and they can run for between 1 and 6 hours at times of peak demand.
Whitacre said he has been told by a major utility provider that at $1/W and a greater than 10-year lifetime, utilities will buy all the storage a company can produce. That means the cost of production must actually be less than that if the storage device manufacturer hopes to turn a profit. “That is a hefty goal and not an easy one,” he said, “and if you can do this, you will change the world.”
Using a simplified economic analysis, Whitacre derived a maximum cost of $5/kg, or under $50 watt-hours (Wh)/kg, for the entire cost of an economically feasible bulk storage device. This calculation took into account the number of cycles required of a relevant device, the amount of kilowatt-hours delivered per cycle, the cost of goods sold, the cost of materials, and the cost of assembling those materials into a device that would be sold in the market. The calculation also assumed that any device would have to cost approximately $100/kWh delivered over the device’s lifetime.
These results, while based on an admittedly simplified analysis, suggest that there is a steep hill for any technology to climb. Lithium-ion batteries, for example, cost in the multiple hundreds of dollars of watt-hours per kilogram, and their total cost of goods is much higher, in the multiple hundreds of dollars per kilowatt-hour.
Moving to higher-energy-density materials could be a solution, but these are typically not as stable. “This is not a law,” said Whitacre, “and I’m hoping somebody finds things that have 1,000 watt-hours per kilogram and can last 10,000 cycles. But in general the more energy you get out of a battery material per cycle, the more transition it has to go through in each one of those cycles, and the less stable it will be over thousands of those cycles.”
Another solution would be to find a battery system that has a low energy density but extremely low cost, less than $5/kg. If this device could cycle rapidly or be more efficient and have a very long lifetime, it could prove economically feasible.
Whitacre is working on an aqueous electrolyte battery that might fit the latter scenario of low cost, low energy densities, and long lifetime. Aqueous electrolyte batteries are based on an old technology. Aqueous electrolytes have an order-of-magnitude-higher conductivity than organic electrolytes so they can be used with thick electrodes that can be much cheaper to manufacture and assemble into a final device.
Lead acid, nickel metal hydride, and alkaline systems are all examples of batteries that use an aqueous electrolyte. Whitacre and his colleagues are developing an aqueous lithium-ion system based on intercalation technologies (Manjunatha et al., 2011; Shivashankaraiah et al., 2011). The electrolyte is typically a neutral pH salt—either lithium nitrate or lithium sulfate—in water. Devices built so far have energy densities in the range of 55 kWh/kg, but most are stable for only hundreds of cycles and their voltage is at the low end.
One device that has displayed stability over thousands of cycles uses a high-surface-area activated carbon anode and an intercalating and de-intercalating lithium manganese oxide cathode (Wang and Xia, 2006). Whitacre explained that he took notice of this system when asked if sodium could replace lithium, since sodium is a much cheaper material. There had been some research on aqueous sodium batteries, but the results were not promising (Sauvage et al., 2007; Zhuo et al., 2006).
Whitacre, however, found that sodium manganate with an orthorhombic structure had very interesting cathode properties. This material, Na0.44MnO2, can be made in a variety of ways from baking soda and manganese dioxide, both of which are very inexpensive. The simplest way to make it is to mix the two starting materials and heat them in a furnace, though they can also be made by sol-gel and hydrothermal processes. The material has a needle-like morphology, is very anisotropic, and can have nanodimensional cross sections. With care, solid-state synthesis can produce high-purity material, contaminated with a small amount of manganese trioxide, that displays suitable properties for a cathode material.
For an anode, activated carbon is the material of choice, but activated carbon is actually a very expensive material, and the cost proposition for using it in a bulk storage device is impossible. To solve that problem, Whitacre has been using molasses as a source of carbon via pyrolysis and then activating it using potassium hydroxide, another relatively inexpensive material. Using a process that preheats the material and then completes the pyrolysis at 800°C in the presence of potassium hydroxide, Whitacre and collaborators generate a material with a surface area of nearly 3,000 m2/g. Electrically, this material has properties that “put it above the laugh test.” He said that if he can make this material for $3 to $4/kg, it would be a viable candidate.
When an anode made from this material is combined with a sodium manganate cathode and aqueous sodium sulfate as the electrolyte, the resulting cell was stable to 1.8 V and could be cycled between 0.4 and 1.8 V for thousands of cycles with negligible loss of capacity and 100 percent coulombic efficiency. The one area in which this cell fell short was in energy density, which was on the order of 15 to 20 Wh/kg versus the 30 to 40 Wh/kg that would make a battery made of these materials cost competitive. However, switching to a cubic spinel manganese dioxide cathode produced a cell that had an energy density of around 30 Wh/kg using very thick electrodes that are extremely stable and easy to manufacture. Moreover, cells made from this material can cycle far more than lead acid batteries.
Aquion, the company Whitacre founded, is now manufacturing batteries using this technology. The cells are encased in industry-proven polypropylene casings using industry-proven sealing technologies. The batteries have a modular product form factor that allows them to be strung together into eight-battery, 15-V modules that can then be stacked and connected in series or parallel as needed. Hundred-volt strings are now in use and 1000-V strings are being tested. The batteries have performed well when tested under conditions that simulate wind power generation over a period of days.
DISCUSSION
In response to a question about the power versus energy demands on a battery intended for use on the grid, Bradwell said that the real issue is the ratio of rated power to rated energy. Batteries for frequency regulation need to discharge for 15 to 45 minutes. A battery can have high power but not much energy and discharge repeatedly throughout the day. To support wind and solar, however, a battery needs to be able to discharge over a much longer period of time. Such batteries would need large energy storage capacity but, at lower power output, would create relatively low-stress demands on a battery. “You still need big batteries, but in terms of how fast you get the energy in and out of the system, it’s not as restrictive,” said Bradwell.
Responding to a question about the energy needed to heat a liquid metal battery, Bradwell noted that, once these batteries reach a certain size, they maintain temperature as a result of the heat generated as the battery cycles. He also noted that these batteries can be cycled at 90 percent efficiency, though at lower current densities.
When asked about the potential for metal-air batteries, Bradwell explained that the main problems with those batteries have to do with the kinetic difficulties in oxidizing oxygen, resulting in inefficient batteries. Metal-air batteries also have limited life cycles based on the experience with zinc-air batteries.
Bradwell was asked about the potential for lithium batteries in cars to serve as load leveling devices for the grid. He replied that in his opinion the negative impact that this would have on the lifetime of the battery would far outweigh the benefits. The battery in a Chevy Volt, for example, costs about $16,000, and load leveling would generate about $1/day in revenue.
In response to a question about what fundamental research needs to be done in the battery field, Bradwell responded that he would like to see modeling work done on the thermo dynamics of liquid alloys. He noted that quantum-mechanical analyses have been applied successfully to crystalline systems, and he would like to see similar work done for liquid alloys.
In response to a question about whether this battery is actually a capacitor, Whitacre said that it is officially known as an asymmetric energy storage device or a “capattery” since it behaves as a hybrid of a battery and a capacitor.
Responding to a comment about how storage devices would be incorporated into the grid, Whitacre noted that a New York utility company recently put out a call for proposals for a peaking gas turbine to supply 1,600 GWh of power, and one of the responses was not for a power plant but for batteries that would be housed in several warehouses distributed across Long Island. The proposal has received high marks despite being slightly more expensive because residents in the Hamptons liked the idea of a warehouse-based solution with no emissions compared to a large gas turbine. The project is moving forward.
Whitacre was critical, in responding to a question about intellectual property protection, of the U.S. Patent Office. He said that patents covering new chemistries are worth very little. What are valuable are patents that control specific ways of using batteries and control algorithms for specific chemistries. Aquion’s patents actually cover the high-voltage strings that the company can make from its batteries. He explained that it is impossible to make such high-voltage strings without using batteries with the performance characteristics of the company’s batteries.
When asked about other promising technologies, Whitacre said that there is some very interesting work being done with lithium sulfur chemistry, which uses simple and inexpensive materials.
In response to a question about what fundamental research needs to be done in the battery field, Whitacre said that he would like to know more about the fundamental nature of pseudocapacitance in different types of electrolytes. He also cited the areas of dendrite formation and dendrite blocking as needing good fundamental research.
- Critical Materials in Large-Scale Battery Applications - The Role of the Chemica...Critical Materials in Large-Scale Battery Applications - The Role of the Chemical Sciences in Finding Alternatives to Critical Resources
Your browsing activity is empty.
Activity recording is turned off.
See more...